News
7 May 2018
ROAD TEST – Adamson S10
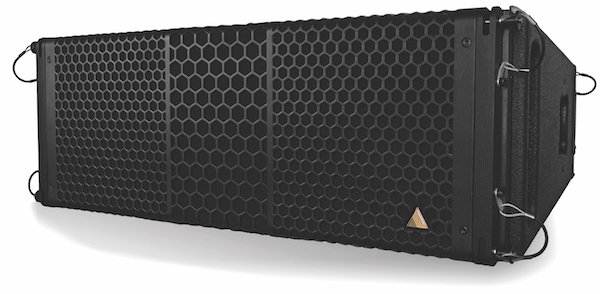
Subscribe to CX E-News
ROAD TEST
Adamson S10
By Scott Mullane.
Scott Mullane is the owner of Brisbane’s Aisle 6 Productions. His current touring clients include The Screaming Jets, Marina Prior, Darren Middleton and 7bit hero, and he has countless record production and recording credits to his name.
Aisle 6 Productions own 16 elements of Adamson S10 and eight S119 subwoofers. We’ve used the system both flown and ground-stacked, and sometimes fly the system with six or seven S10 elements per side because of venue trim height or low load rating restrictions. Ground stacking sees us setting it up with four S10s mounted two subs a side.
DESIGN
The S10 is aesthetically very pleasing, and this detail in design has flowed through to the engineering. What impresses me are the simple things; for example, the speaker grille only has four screws.
A lot of manufacturers have larger amounts of screws to stop grille rattling, but this makes it tedious to remove. The way Adamson have designed the horn flare, the grille clips over the extension of the flare and then screws to the timber so it’s supported in many locations. It’s clever little things like that which really impressed me straight away, and there are quite a few.
FLYING MADE SIMPLE
The first time we used the S10 system, we flew it, and it was surprisingly quick. A colleague of mine recently commented that he’d seen the system pulled out of a venue’s roof, loaded, and packed in the truck before the stage crew have even finished packing the stage down.
If you do some preparation using Adamson’s Blueprint AV software, you can print out notes for riggers with the loadings as part of your documentation for the show, and pass on cabinet angles as documents to your staff.
What physically makes loading easy is the fact there’s four top boxes on each dolly and one person can set all the recommended box angles in the factory literally with one arm tied behind their back. There is physically no box lifting to re-pin the angle positions – you slide a slider into the correct position, and put the pin back in.
The only thing moving is a slider, not a weighty cabinet. You get to the gig, wheel the dolly forward to pick-up point, hook it up, and lift it into the air. It expands into the curve that you’ve created, then you put the next four under it and link them up. It’s literally that easy.
Also, there’s no fly-frame needed when you ground stack an S10 rig. You put the mid-highs on top of the subs and the hardware is coupled together with pins. No inverted fly frames. Patching the boxes is simple too – using NL-8, you patch into the top or bottom box, and then load the amps in sequences of four cabinets. A cross-over cable then patches between boxes four and five.
THE WEIGHTING GAME
I really like what Adamson has done in Blueprint AV with the weighting for performance prediction. They’ve got the regular A, C, and flat or zero weightings, but they’ve created their own weighting, which they call ‘Y’ weighting, which measures from 2kHz to 8kHz. It’s really focused on vocal intelligibility and projection.
Over the throw distance Adamson recommend that from front to back you don’t have any more than a -6 dB roll-off. It’s interesting to see what happens when you check Y weighting setting against A and C weighting. The Y weighting really does make a great starting point.
MIXING, EQING, AND SOUND QUALITY
Mixing on an S10 system requires a head-shift, in that you can’t just walk up to it and start mixing like you’re on any old PA. To really get the most out of it, you have to stop for a moment, listen to what’s going on, and respond to what you are hearing. It is just so clean.
For most of the shows we’ve done with the S10, including the acoustically terrible Suncorp Piazza in
Brisbane, we load the basic Adamson configuration pre-set and end up running no FOH EQ. We might notch out one frequency now and then, but any tweaking is more about coverage.
I also find that I’m using less channel EQ as well. The factor that causes the head-shift I mentioned is the lack of harmonic distortion, which makes the S10 incredibly clean, while producing high SPL. One or two engineers we’ve sat with as they’ve mixed on it have said “It doesn’t go very loud, does it?” We then just show them a meter reading! Their brains are not processing it as ‘loud’ because there’s no distortion. It’s very clean, so it’s very revealing.
You’ve really got to create the tones that you want to deliver, which is obviously what we should be doing when we mix. It brings out the creative workflow, as opposed to the usual guerrilla warfare of trying to battle problems in the mix. The mid-highs are great, but the subwoofers have particularly impressed me.
The S119 subs are very good at producing the fundamental of the material. In most subs, you’ve got your fundamental tone, but the harmonics of that fundamental are not much quieter than the fundamental note itself. It seems to me it must be difficult to manufacture a sub that is not adding too much unwanted harmonic information into its output.
The S119s deliver the same SPL across a broad sub spectrum only reproducing the notes you’re putting in, with the harmonics attenuated below the fundamental quite a lot. Therefore, if you want to hear 40Hz, you’ve got to create 40Hz, not just ‘wobbly stuff’ that’s harmonically relevant.
WEIGHTS AND MEASURES
As part of our research before purchase, we compared the size, weight and power output of the major line arrays in the market. Putting all biases about brand aside, everything we found that had an equivalent output to an S10 was 10 kilos or more heavier and 10 centimetres or more larger per element.
We looked at the specs of accessories like VMB towerlifts; you can’t hang eight elements of most high-output line arrays on those. But an eight-a-side S10 rig with a fly frame weighs 238 kilos, which is within-spec.
The two-way design means less amplifier channels when bi-amped, making the whole system slightly more affordable, and it’s all less weight in the truck. Weights and measures really add up – it’s an interesting experiment do across all brands; audio fidelity and sound quality can be subjective things, but weights and measures are fixed.
SUGGESTED IMPROVEMENTS
I’d like to see more configuration presets available in the processors. For example, for when we run six or seven elements aside and use two elements for front-fill. With a line array it’s not as simple as point-and-shoot, so you do need to be a little bit more sophisticated about set-up or you won’t get the result you want.
I have been reticent to try things that are ‘outside of the Adamson box’, but I believe the new advanced Adamson training that’s been announced will empower me with more knowledge to set up more advanced configurations.
Brand: Adamson
Model: S10, S119
Pricing: P.O.A.
Product Info: www.adamsonsystems.com
Distributor: www.cmi.com.au
This article first appeared in the print edition of CX Magazine May 2018, pp.59-62. CX Magazine is Australia and New Zealand’s only publication dedicated to entertainment technology news and issues. Read all editions for free or search our archive www.cxnetwork.com.au
Subscribe
Published monthly since 1991, our famous AV industry magazine is free for download or pay for print. Subscribers also receive CX News, our free weekly email with the latest industry news and jobs.