News
8 Nov 2023
The P.A. People Discuss Venue Engineering
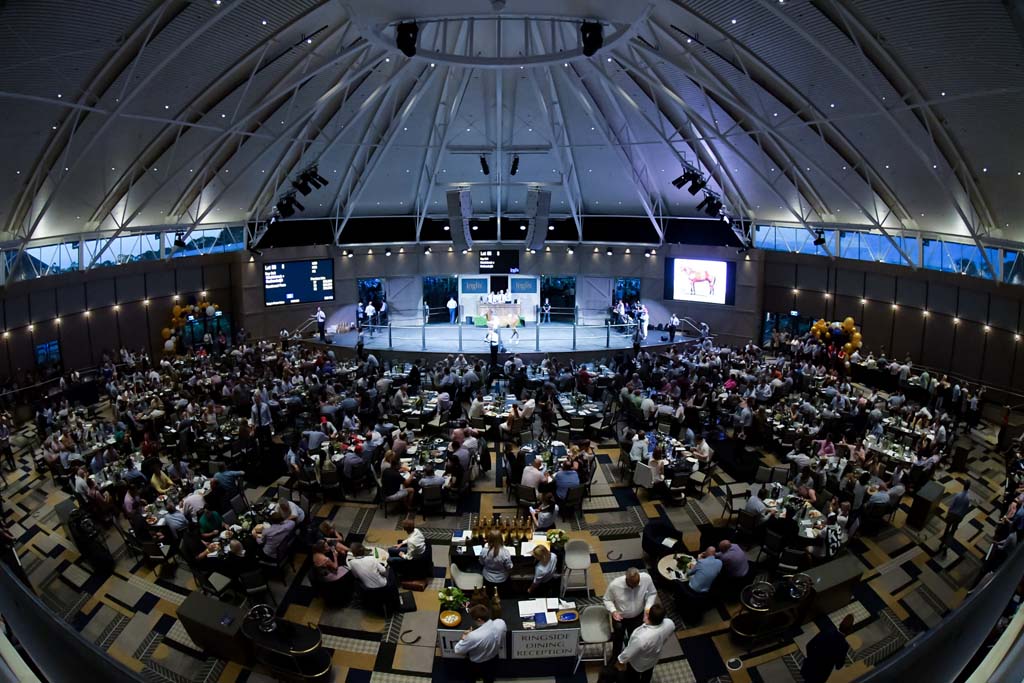
Subscribe to CX E-News
Safety, Experience, Equipment & Capacity
The P.A. People’s venue engineering team has over 200 years of combined experience across engineered design, integration, installation and service. With standards-compliant tools and products, the company can provide solutions appropriate to venue type, a range of operational demands and end user groups.
Peter Grisard, Manager – Venue Engineering for The P.A. People says: “In this business, we must constantly remind ourselves that we lift, suspend and move significant gear over performers and audiences, making the issue of fit-for-purpose gear and people paramount.”
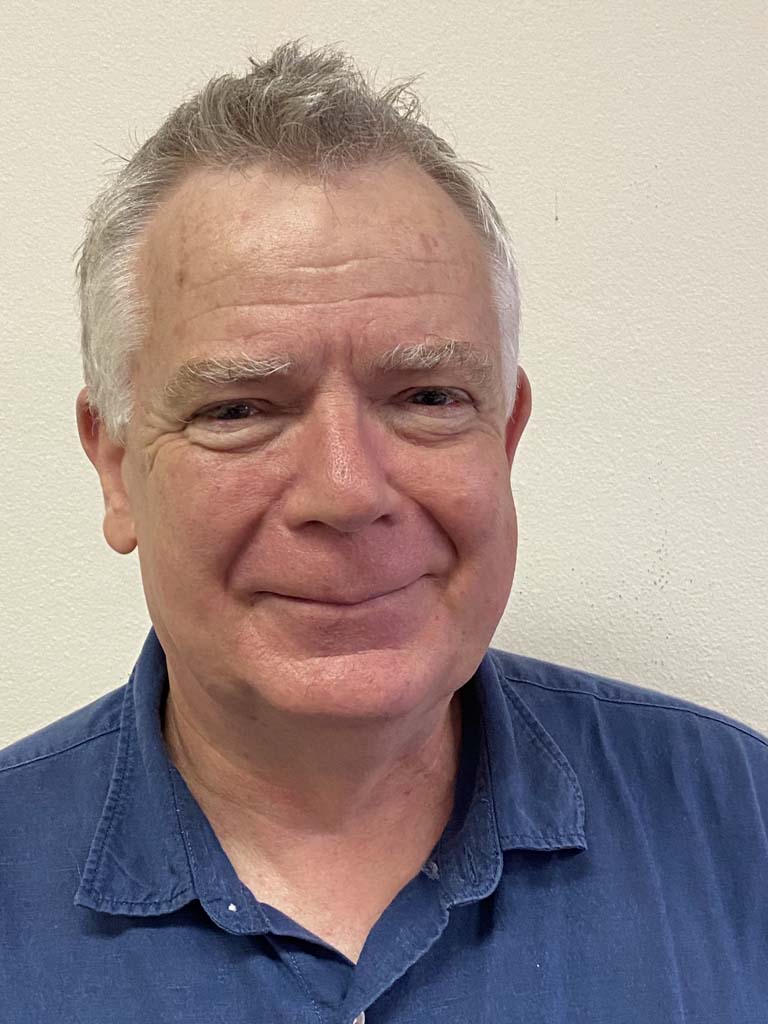
At the 2023 Integrate Expo in Sydney, and the ENTECH Roadshow, which recently toured five capital cities, The P.A. People participated in an education program with discussions on ‘Safe Workplaces – Your Duty of Care’. These were led by The P.A. People’s Peter Grisard, Andrew Mathieson – Chief Engineer, and Tim Pike – Service Manager, QLD. Some of the issues discussed here included: duties of a PCBU under Safe Work Australia, machinery inspections and maintenance, the safety of ‘unknown’ machinery, and service provider/ certifier types of testing.
Andrew Mathieson said: “We field innumerable questions from venue operators, where they’ll typically say things like: ‘We’ve always done it this way, nothing’s changed. What’s the problem?’ or ‘Just certify this; we want someone to come in and say it’s okay’. Others will ask, ‘There’s a new safety standard, so does my machinery need to be retrospectively brought up to this new standard?’ Overall, there’s a great deal of knowledge and experience in the industry, but when it comes to compliance with codes and standards there’s less clarity and understanding.”
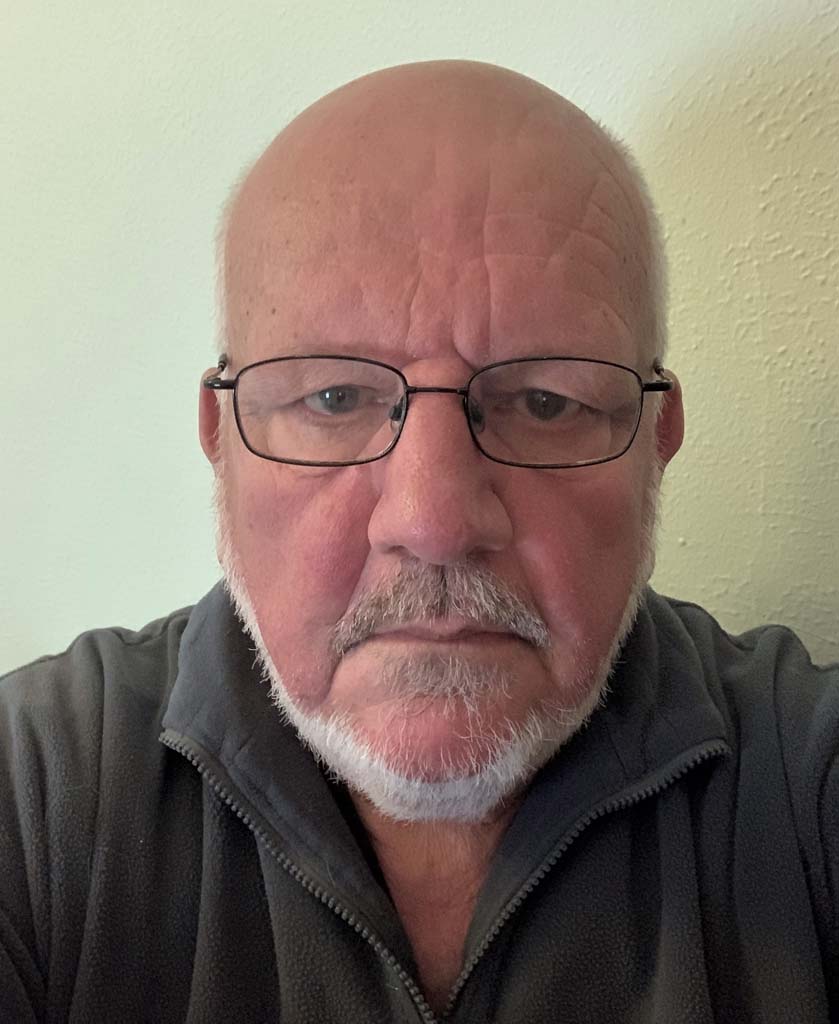
Peter Grisard continued: “Some situations include old machinery that might have been there 25 years that is clearly in a pretty poor state, has no service history or documentation, and where the client is searching the internet to find information on their gear. But generally, venues are becoming increasingly aware of their responsibilities from a WHS point of view, and we’re being asked to service and maintain equipment and certify it.
Respectfully, I find sometimes clients don’t quite know what they’re asking for, or their understanding is lacking, so you have to be prepared to say, ‘Perhaps this is not such a good idea,’ or ‘Maybe you should consider doing it differently’. Part of my role is to sit with clients, gather up the information and bring it back for discussion with my colleagues about feasibility and risk – that’s a real issue for us. The exercise is about listening – and I spend quite a deal of time listening to our engineers – about what’s wise, what’s not, what design choices we have etc. Before you do anything, it’s vitally important to seek the advice of an appropriately qualified venue engineering professional.”
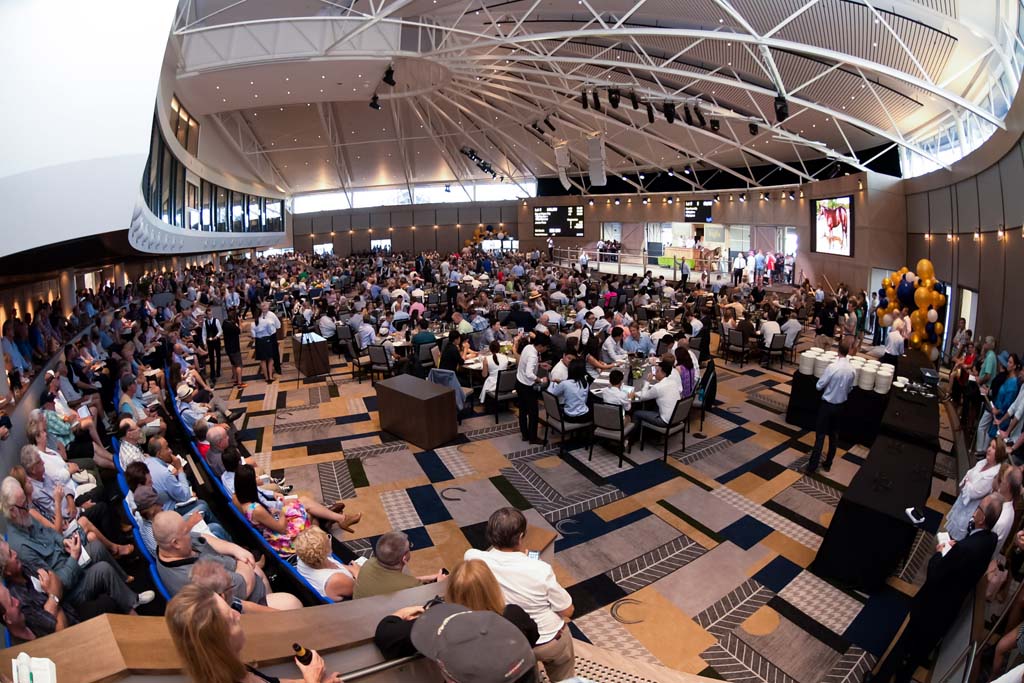
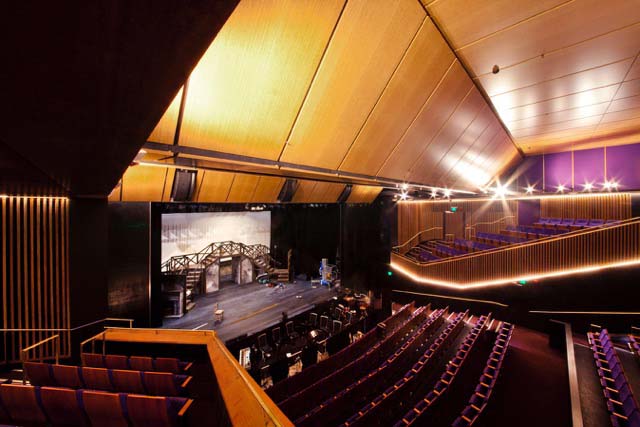
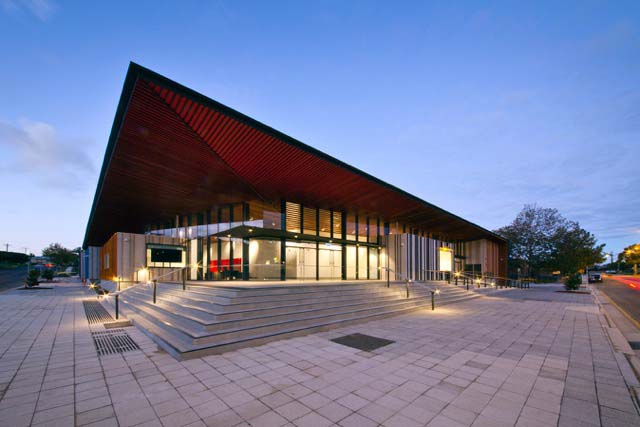
Chris Dodds, Managing Director of The P.A. People commented on current opportunities and challenges: “Coming out of COVID, and having been fortunate to retain our key staff, we took the view that once venues re-opened, engineered solutions would again be in strong demand. Projects that may have been paused would come on-stream again as supply chains regained traction. So we took action on several fronts to ensure that we had capacity to respond. Our value-add and fit-for-purpose philosophy meant that we were careful in our choice of work and active in securing trusted product supply partners. This has led to several announcements in the past two years, where we’ve invested substantially in a dedicated venue engineering team, product representation arrangements with world-leading venue equipment manufacturers, and of course, our acquisition of TheatreQuip, with its own 30- year history, local expertise, and growing product range. With arguably the most experienced team in the country – across design, integration, installation and service – we are equipped to comprehensively advise venue clients on solution options that are appropriate to their needs. By way of example, just recently a major task in the venue engineering space involved an orchestra lift, acoustic baffles and reflectors, and an 18-line grid system; a significant project and solution for that client, and two other projects requiring the retrofitting of new counter-weight flying systems.”
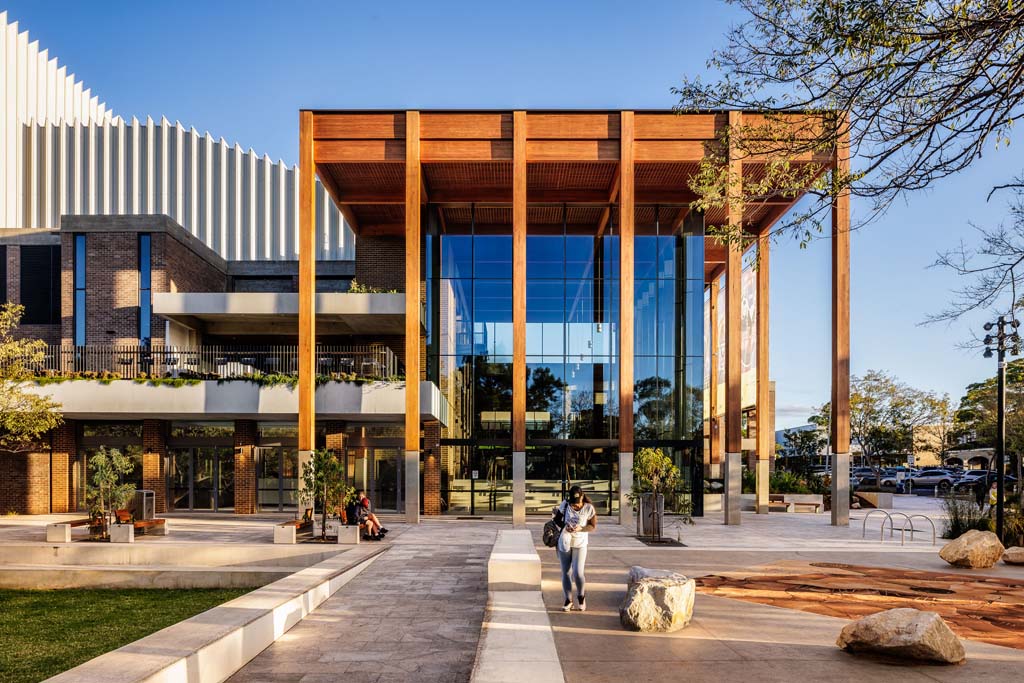
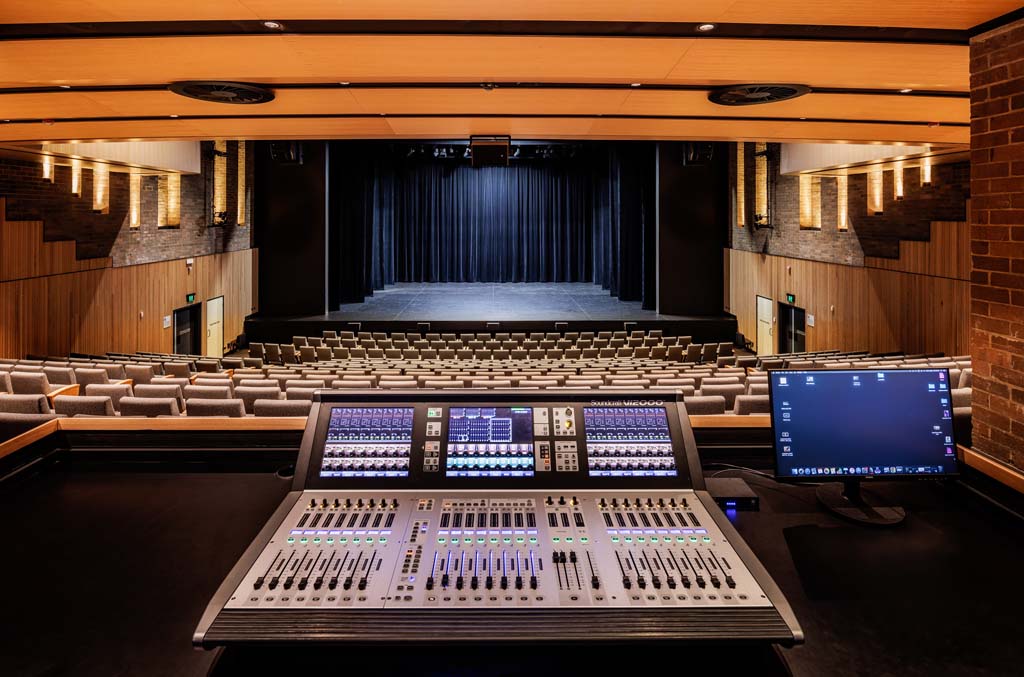
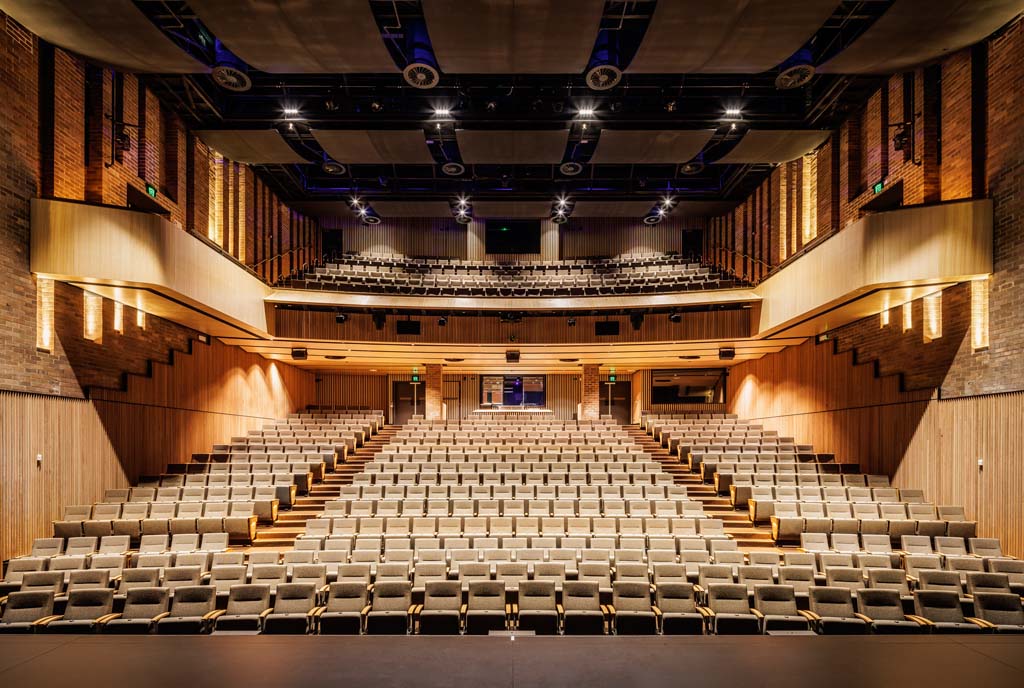
Chris continued, adding that, “Regardless of the context, it’s essentially always about live performance. Whether it be a new installation, rental or service, our expertise is to understand what you need, and what’s required to deliver that result.”
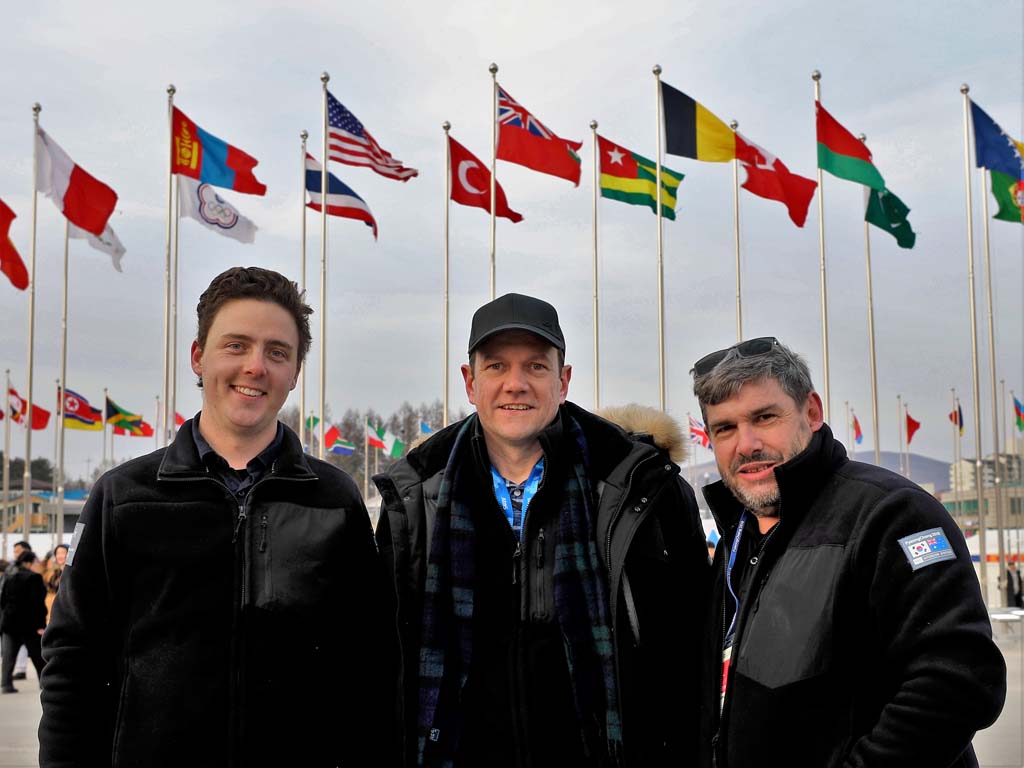
Pointing to added capacity achieved in the last 18 months, Chris explains; “Expanding our local manufacturing capability allows us more flexibility, choice and range. Adding to our existing TheatreQuip products, we’ve now designed three drum hoists, a pile wind hoist and several new lighting bars; we’ve established a comprehensive sewing room which assembles theatre drapes, curtain legs and backdrops. Adding this to our leading-brand representation for chain motors and control from Movecat, rigid chain actuators from Serapid and motion control tools from Teqsas, we have a suite of components and options that we can employ. It’s about finding the right solution for the customer to deliver what they need.”
Subscribe
Published monthly since 1991, our famous AV industry magazine is free for download or pay for print. Subscribers also receive CX News, our free weekly email with the latest industry news and jobs.