EVENTS
30 Apr 2024
GTXtra
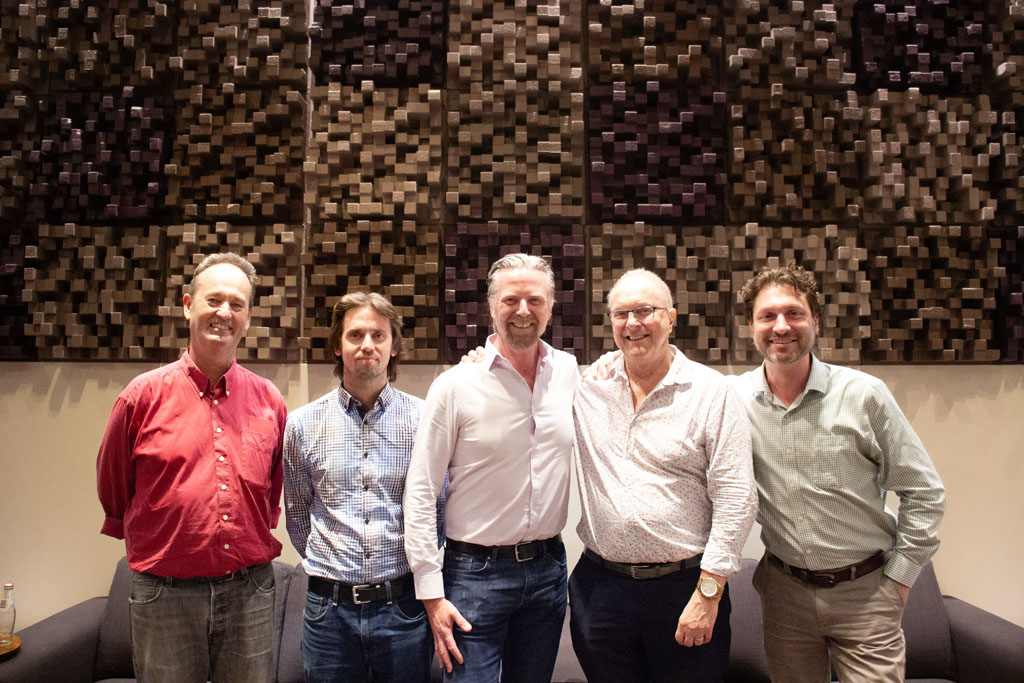
Subscribe to CX E-News
A Meeting of the Minds
Not even a week after the GTX event documented earlier, Group Technologies hosted a much smaller, but just as influential affair at their HQ. The group of electroacoustic consultants collectively known as ICE Design were invited to learn all about GT’s audio brand Quest Engineering, designed and built in-house, and visit the last remaining loudspeaker driver manufacturer in Australia, Lorantz Audio, who supply Quest.
ICE Design is made up of three separate businesses and their staff; Glenn Leembruggen’s Acoustic Directions, David Gilfillan’s Gilfillan Soundwork, and Mark Hanson’s Hanson Associates. Until late last year, Rod Louey-Gung’s Integrated Media was also part of the group, but Rod announced his retirement in October.
Collectively, ICE Design have been responsible for the electroacoustic and AV designs of some of the region’s most complex and consequential projects; High Courts, Supreme Courts, Parliaments, airports, universities, stadia, government buildings, museums, and more. ICE are known for such exacting audio performance that if a product doesn’t exist that meets their requirements for a specific project, they’ll design and build one.
I caught up with Glenn, Mark, David, David’s associate James Love, and Group Technologies’ Director of Sales Shane Cannon just as they had returned form the Lorantz Audio factory in Dandenong, in south-eastern Melbourne. The consultants were buzzing as only those with a deep love of audio and respect for quality could be.
“I’ve been around transducers a little while, as you know,” observes Glenn. “But I’ve never seen one being made. Lorantz are making their own cones and spiders (the support structure that keep the voice coil and cone aligned – Ed.). The wealth of knowledge at Lorantz is profound. Their General Manager, Mikhail Barabasz, is in his 70s, and we want the knowledge he has to continue. There needs to be recognition of the skill that’s there.
He’s got all the best test equipment, showing loudspeaker distortion curves, how the suspension and magnetic field can become nonlinear, and why one design is better than another. He makes it all come alive.”
“Lorantz are building two particular drivers for the Quest subwoofer range,” adds Mark Hanson. “That was a complete eye-opener for me. I thought a driver was a driver, just a bit of paper or something else for the cone.
To experience first-hand the decades of knowledge that’s gone into refining the drivers that are used in Quest products was just fantastic.”
Quest Engineering
Quest design, manufacture and test loudspeakers and amplifiers at Group Technologies’ facility; the same building that hosts their demonstration rooms, offices, and warehouse. Quest’s range includes loudspeakers for any kind of installation, matched with amplifiers, mixer amplifiers, DSP, and rigging. You see Quest products in almost every market sector in Australia, and they export a significant amount overseas.
ICE Design got to peek behind the curtain at Quest’s operation in Pascoe Vale, including their anechoic chamber, testing facilities, and assembly line. That was followed by listening sessions across the Quest, RCF, and Nexo ranges.
“I really get a sense of the passion Group Technologies has for Quest,” notes David Gilfillan. “Because they’re making it themselves, it becomes really special.”
“I’m thrilled that an Australian company is doing this level of work with this level of investment,” Glenn relates. “It’s been amazing to see what you have to do to make a product that’s more than the acoustics or the electronics. It’s exhilarating to understand that we have an audio manufacturing industry in Australia. The Quest electronics are beautiful, and world class. It’s really exciting to see that they’re performing so well on the world stage.”
“Through ICE, I’ve learnt a lot over the last few years about making your own equipment; whether it’s for reproducing, testing, or measuring audio,” elaborates James Love. “To actually see people who are doing it within a large-scale product manufacturing process is a real eye-opener.”
“I’ve learnt a hell of a lot today,” reports Mark Hanson. “I’ve learnt a lot from my colleagues over the years in terms of how you put a finished product with measured performance into a space. But to really appreciate what goes into building, designing, and manufacturing audio products; the practical challenges you’ve got to overcome, making sure grills don’t fall off or go rusty, for example. There’s so much to it.”
So, how has experiencing Quest’s presence influenced how you would approach a system design? “When you respond to a tender or you’re designing a system, it’s easy to go back into your established patterns,” admits Glenn. “At ICE, we don’t go back into our patterns when it comes to acoustics; we’re always in first principles mode. When it comes to electronics, I think I have a tendency to go back into my patterns because of history and supplier relationships. I think it’s time to break out of that. We’ve seen evidence of product here that shakes you up and says, ‘come on, look at this stuff!’ I’ve known of Quest for a long while, but I never really understood how serious it all was, really.”
“From a Group Technologies perspective, it was great to have the ICE Design team in,” concludes Shane Cannon. “While I only met James last year, I’ve known the rest of team for 25 or 30 years. It was great to bring in the brains trust of our industry, who have all been working at the top of their game a long time, and are very passionate about it. It’s an opportunity to not just share what we’re doing with Quest, but then get feedback as to what products the market needs, where the gaps are, and what is missing. We’ve demonstrated what we do, the passion we do it with, and the capability of the products.”
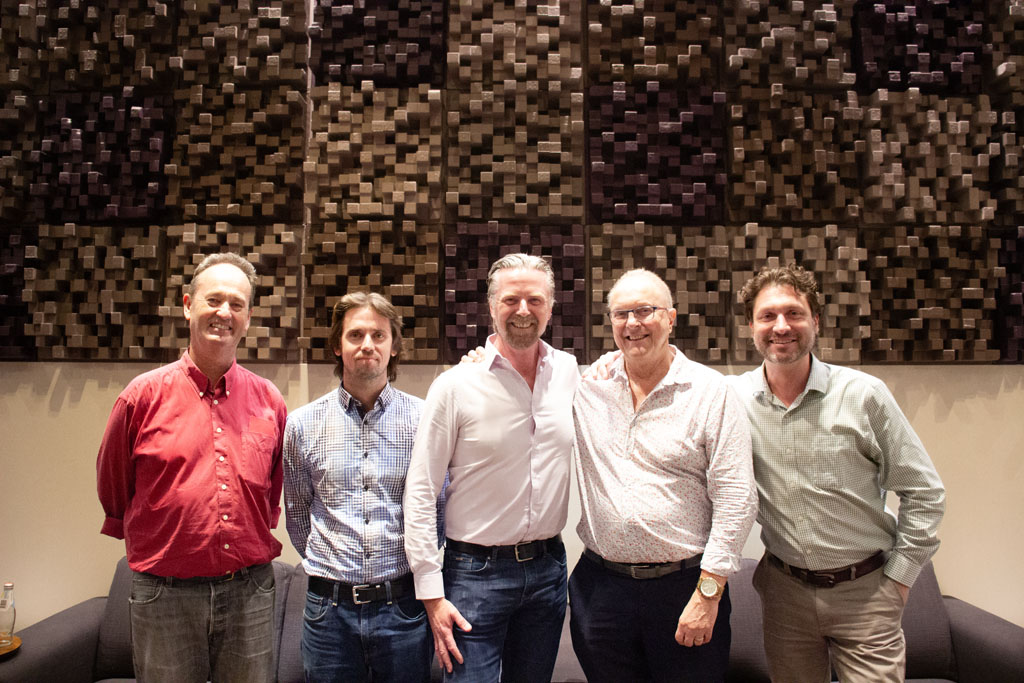
Subscribe
Published monthly since 1991, our famous AV industry magazine is free for download or pay for print. Subscribers also receive CX News, our free weekly email with the latest industry news and jobs.