RETRO
16 May 2023
How a humble microphone dominates live sound
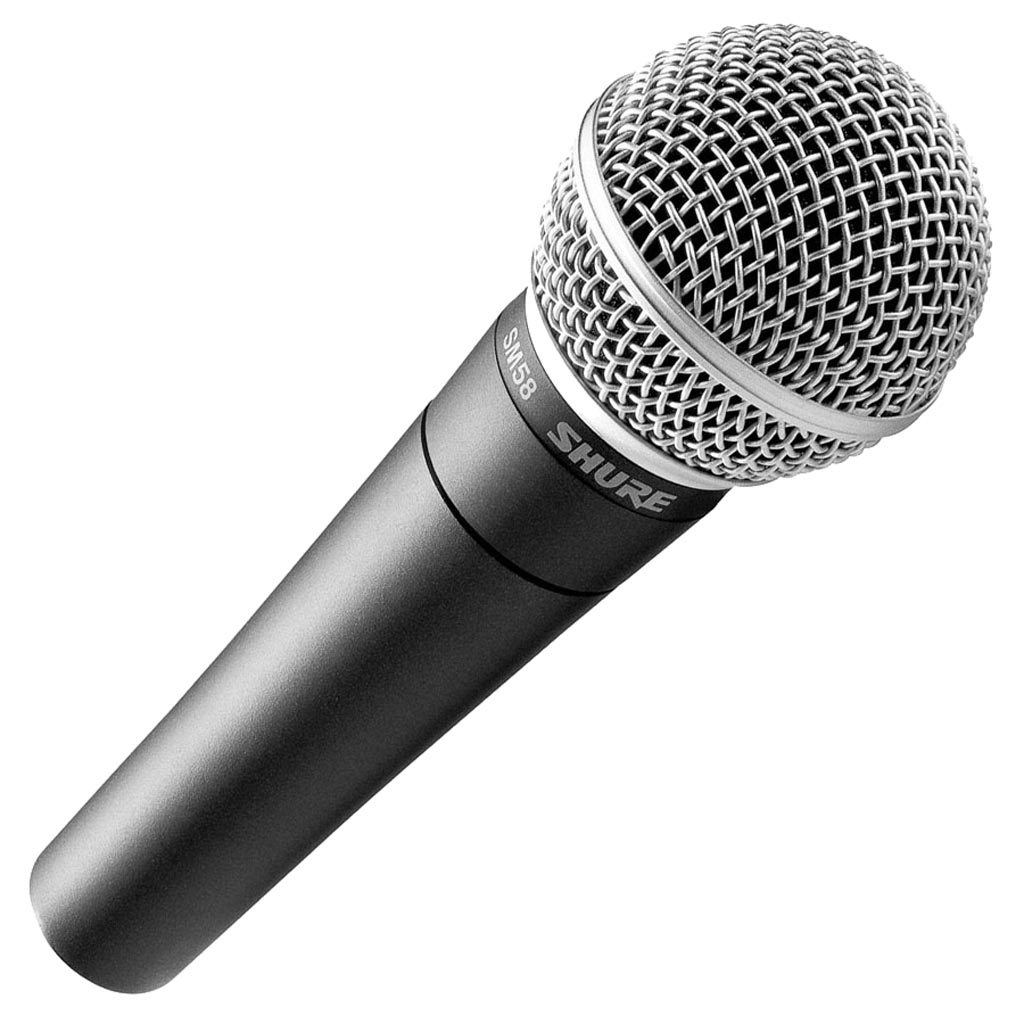
Subscribe to CX E-News
/ ODE TO THE SM58
At Shure HQ in Chicago, they don’t really know how many SM58 vocal microphones they have shipped since their introduction in 1966, but it must be well over a million. The SM58 is the top selling hand-held vocal dynamic microphone in the world. This makes it the single most successful product in the history of professional audio, if you don’t include the XLR connector.
Intrigued at why the SM58 continues without impediment, I had a look at the history and also at the way they build and design things at Shure.
Radio Parts
In the 1930s, Mr. S. N. Shure diversified his radio parts business to design and build a microphone. In the Great Depression, his radio business had declined, and he took on distribution of a microphone, which gave him the idea to design and build a better one.
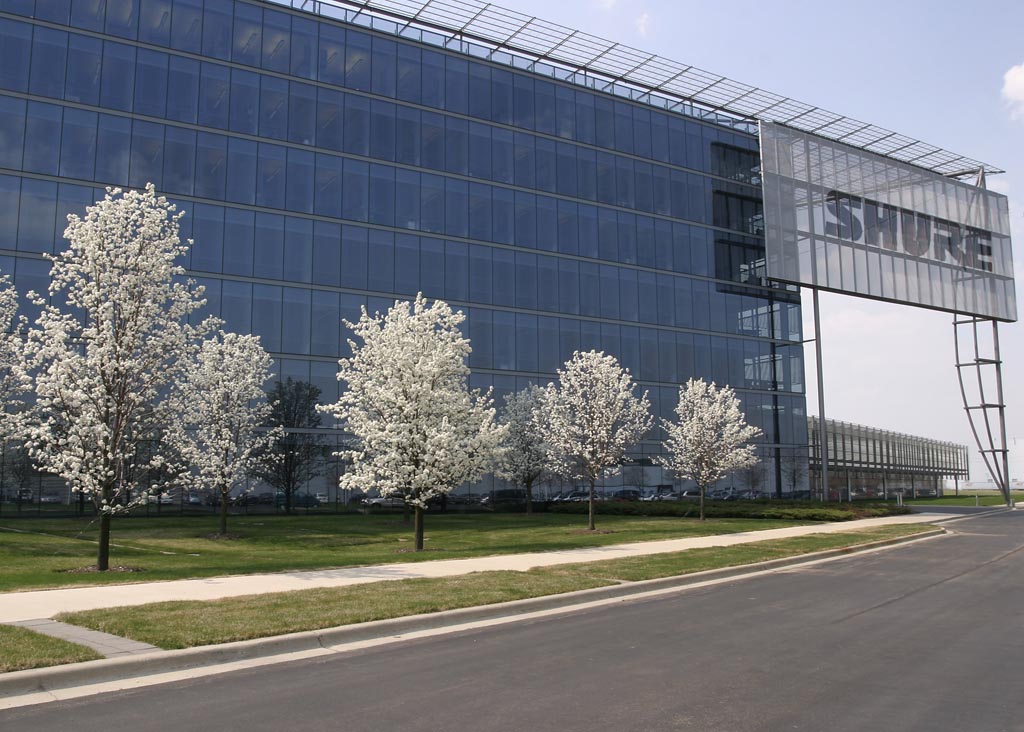
Thus in 1932 they launched the Model 33N Two-Button Carbon Microphone. A short while later, in 1939 they launched the Model 55 Unidyne Microphone; the first single-element unidirectional dynamic microphone. That single-element design made for a smaller microphone which was less expensive, and, therefore, more accessible to all. Then the Second World War got in the way, and the company built airplane headsets, pilot throat microphones, and navy ship microphones around the clock.
Then in 1959, the Unidyne III Microphone was the first high-quality unidirectional microphone to be used by speaking into the end (“end- firing”) rather than the side of the microphone. It was the predecessor to the SM57. By 1966, the SM57 (adapted from the Unidyne III a year earlier) was joined by the SM58. The round windshield minimised popping and provided a safety screen for the cartridge.
Design Hurdles
Chad Wiggins is the Category Director of Wired Products. He told CX that the microphone housing is same then as is sold today. “In 1964 we made significant technological advancement with a sophisticated shock mount. This allowed the capsule to be housed in a handle. It’s called the Pneumatic Shockmount; we haven’t seen any dynamic microphone that has been able to duplicate its performance attributes. Now the mic could be handheld, a self-windscreen mic with a ball grille. It was the world’s first ice cream shaped mic and thus the blueprint for everything we see today.”
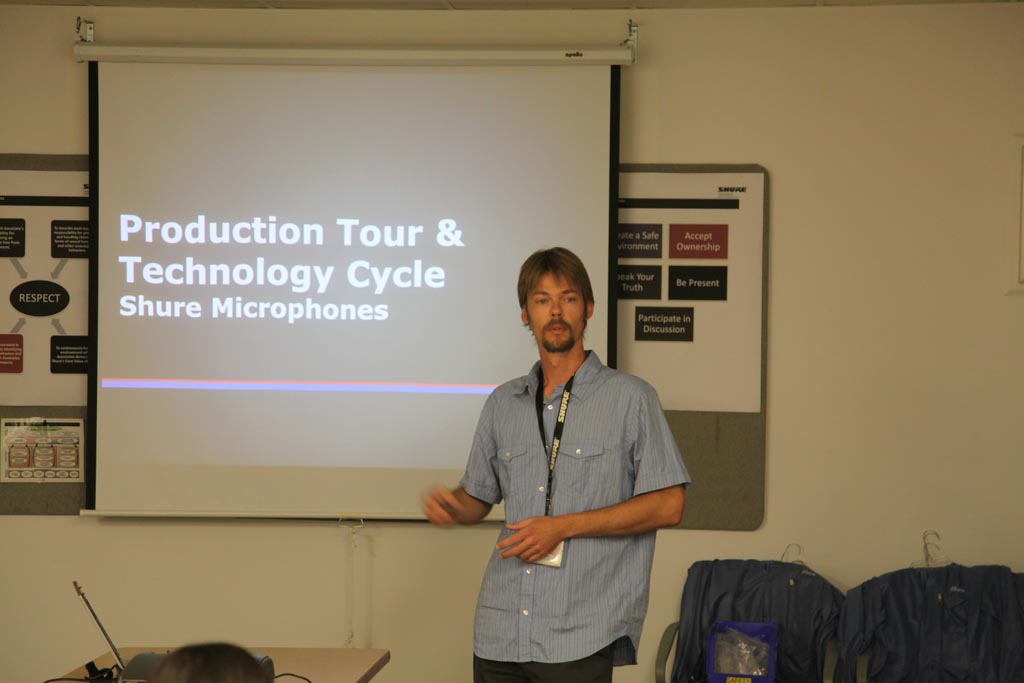
Chad explained that back in the 30s, Shure created a unidirectional pickup pattern by introducing a port in the rear. They studied and resolved pattern control, because feedback was a recognised problem the minute anyone amplified anything and introduced a microphone.
Then there is the chamber behind the magnet assembly, known as the rear cavity. “The cavity volume behind the capsule influences low frequency response. It damps the diaphragm. The resonance frequency of an SM58 is 125 Hz. A second chamber is included behind the first, and only in our pneumatic shockmount. There is another resistance between the two chambers. The whole assembly then is mounted on a specifically tuned rubber part. Then all you need to do is to stimulate the diaphragm with sound!”
Every production run is audited carefully. “Every small change makes a big difference to performance”, concluded Chad.
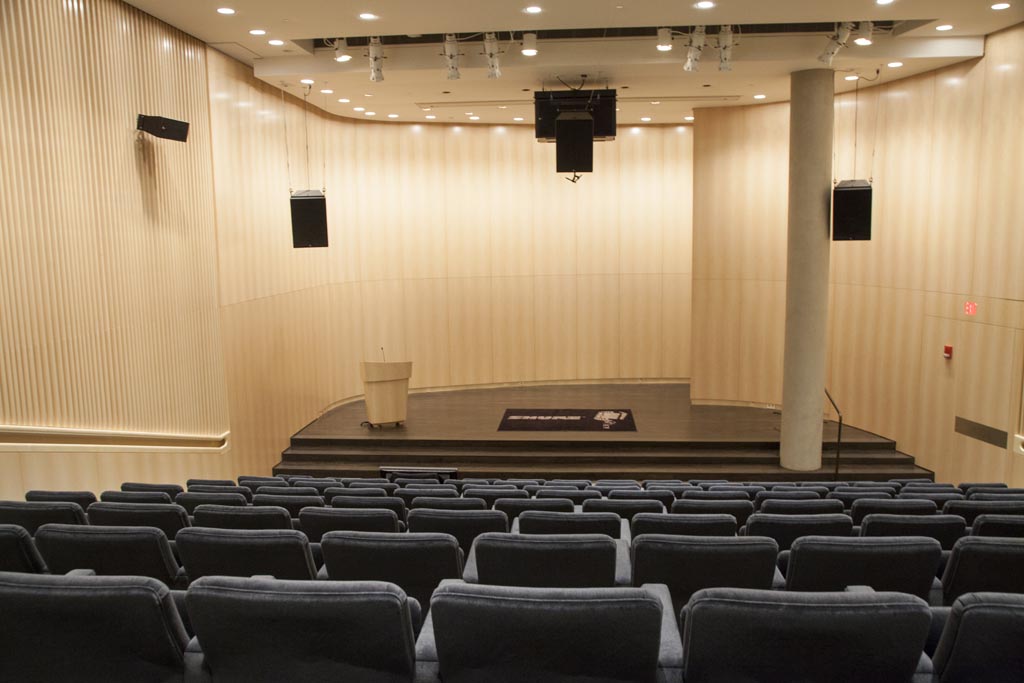
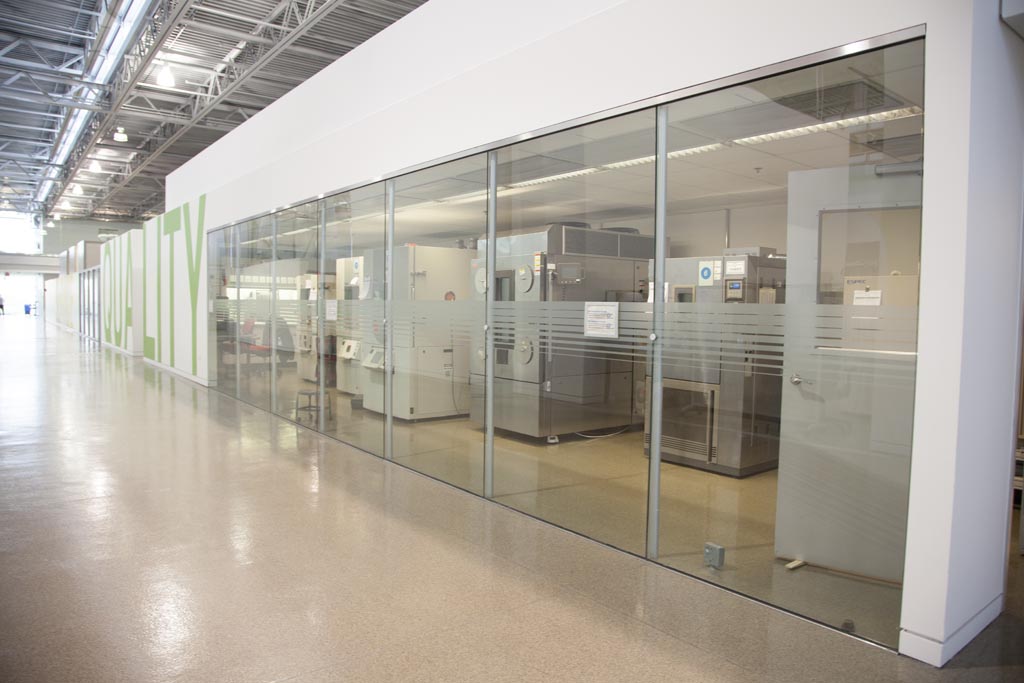
Surprising Testing
Shure HQ is at West Touhy Avenue in Niles, a satellite of Chicago in what they call Chicagoland. The building is very impressive; seven floors, massive glass façade, all fashioned by a German architect for a merchandising company that diversified into dot coms in the 1990s.
They went bust with the dot com crash, and Shure came along in 2006 and paid 30% of the construction cost. Then they added on a technology annexe, in effect a tall space that extends out the back for a couple of football fields or so. The glass and concrete finish was matched up to the main tower.
In the massive foyer are rows of exotic plants; when I was there bromeliads featured. I asked about this. It transpires the owner of Shure is Mrs Shure, widow of the founder. She purchases the foyer flowers and shrubs on her own account, and every six weeks or so they are changed out. The retired flowers and shrubs are carefully packed in cardboard carry cartons for the staff (called associates) to take home.
There is a massive atrium in the foyer, with three glass elevators. It is easily the most impressive manufacturer building I’ve been into, within our industry.
Out in the Technology Wing, I get the tour and meet Lane Dulaney, the director of corporate quality. He is both revered and detested across the marketing, design and sales floors since he alone must sign off EVERY new product.
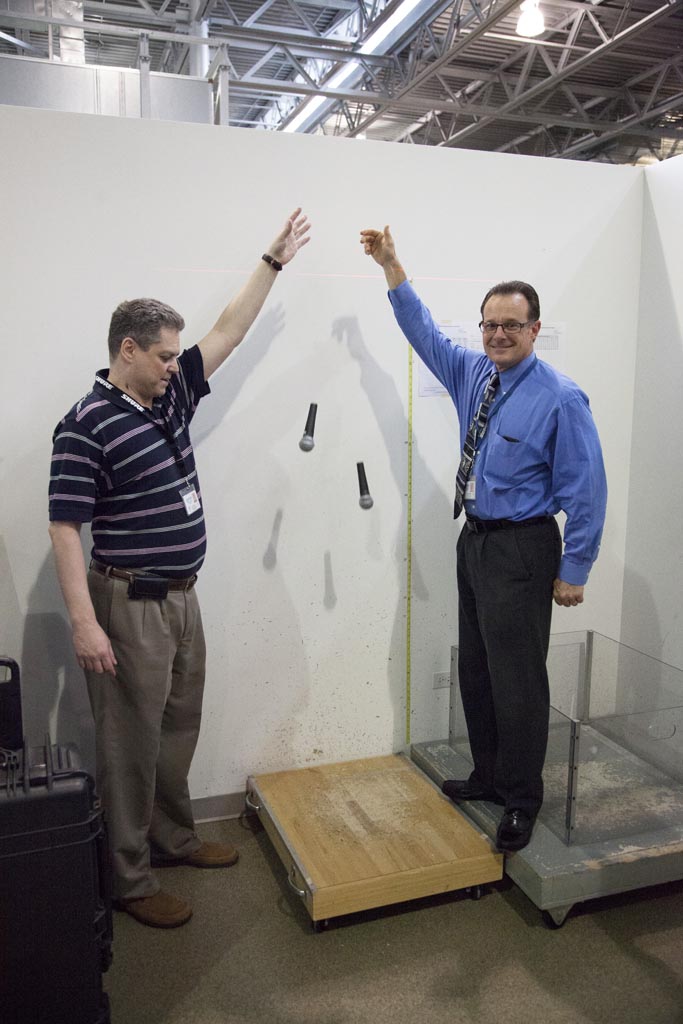
While the procedures will surprise you, it transpires that the original SM58 went through something similar since Mr. Shure transitioned the whole firm to conform with military standards numbers 810 and 202 in order to build during the war.
After the war, some questioned the need to maintain manufacturing to these standards. He stood firm, and today the firm still adheres to these standards. It is eye opening.
We Make Sweat
Shure have built their own test tools, like the sweat machine. In all seriousness they analysed sweat scientifically and had a formulation created that comes in big gallon bins.
A machine sprays sweat into and onto products, which makes a unique test for synthetic perspiration. The machine has a Shure part number, and there is one at each of the three factories around the world.
How would you test microphones and electronics? Heat and cold are easy, Shure go from minus 29 degrees to plus 74 degrees Celsius, which is extreme by any measure.
All products are tested in research and development, and all products have to pass all the tests before Lane Dulaney will sign them as good for production. Then various products are random tested from production batches to ensure there is no quality fade.
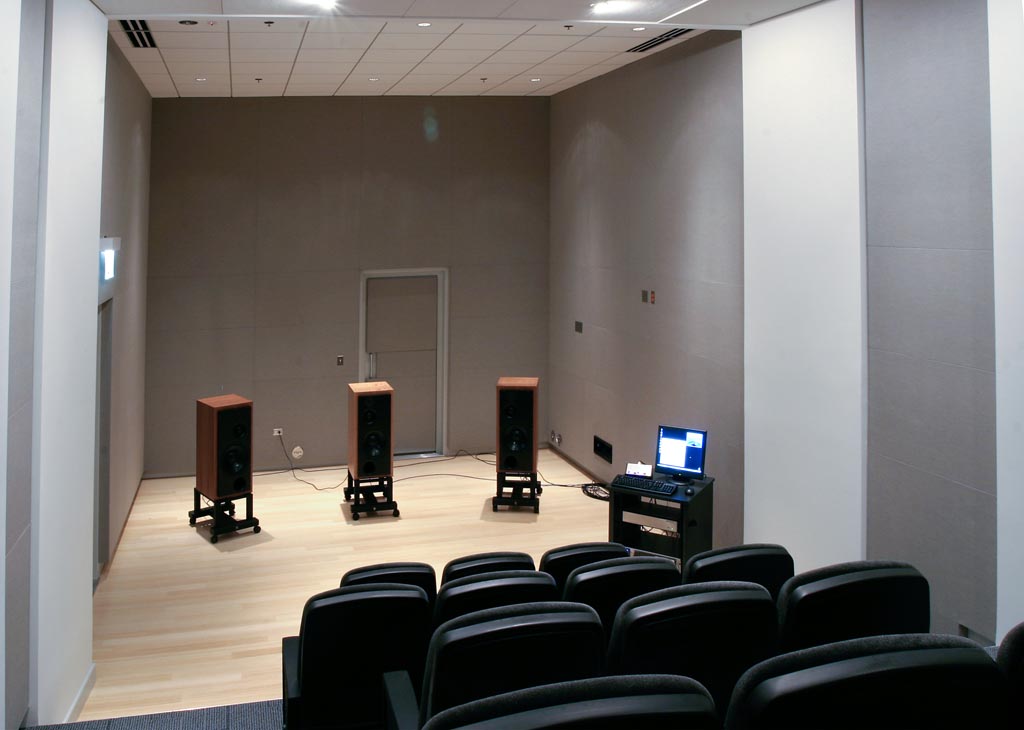
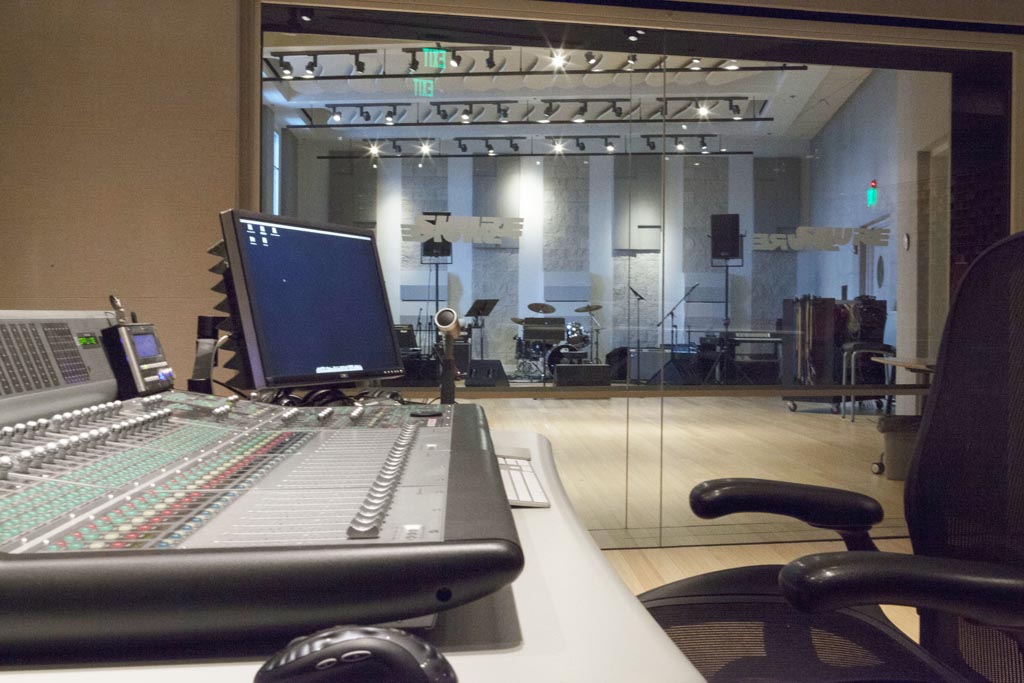
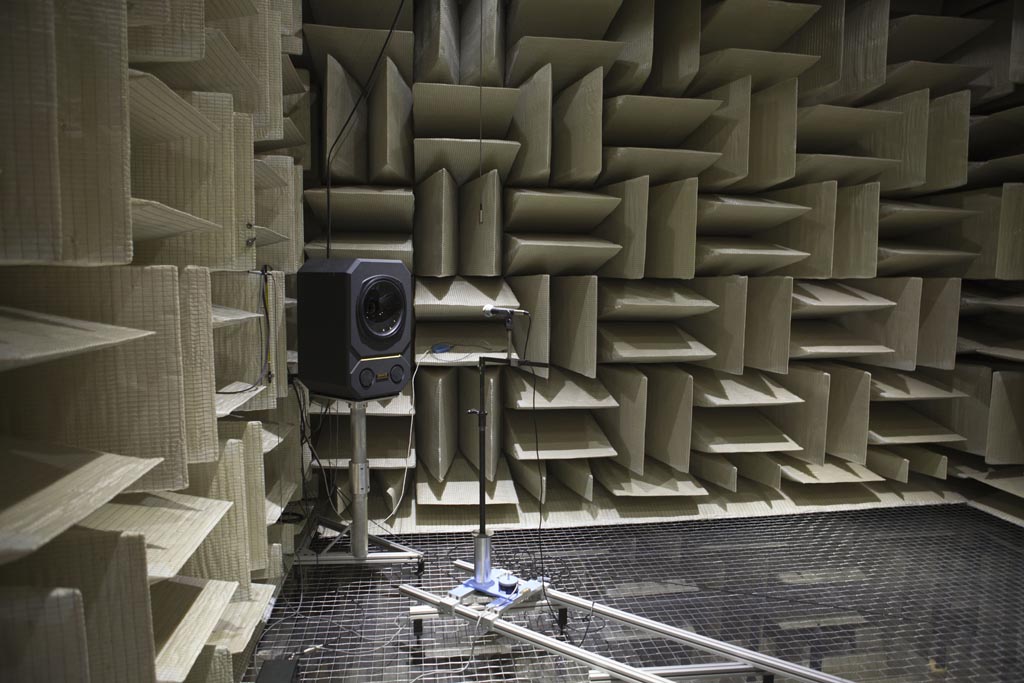
Minute measurements are taken, panel printing is examined under microscopes, for position and precision. There is a salt fog testing chamber, a switch cycler for electronic devices, and a cable flex test machine that will find the weak point on any cable. Once the product fails under load, an x-ray is taken to find the point of failure.
How about solar radiation? A ten day cycle emulates 20 hours of sunlight a day, for a highly accelerated test. Indeed the acronym HALT or Highly Accelerated Life Test is used a lot. They blast nitrogen on the product while it is being vibrated. The philosophy is to find a fail point, fix it, then find another, fix it, and repeat. “We invest in critical reliability”, said Lane.
Boris Libo shows us the drop test, which is quite simple. All products including KSM ribbon microphones undergo a two metre drop onto a hardwood floor, and on to a concrete floor, a total of ten times. Frequency response is checked each time.
Listen Up…..
John Born is the Product Manager for Wired Products. He showed CX through the audio measurement facilities at Shure, starting with the anechoic chamber. Another Shure test machine pivots a microphone in a semi circle, a few degrees at a time for quicker measurements.
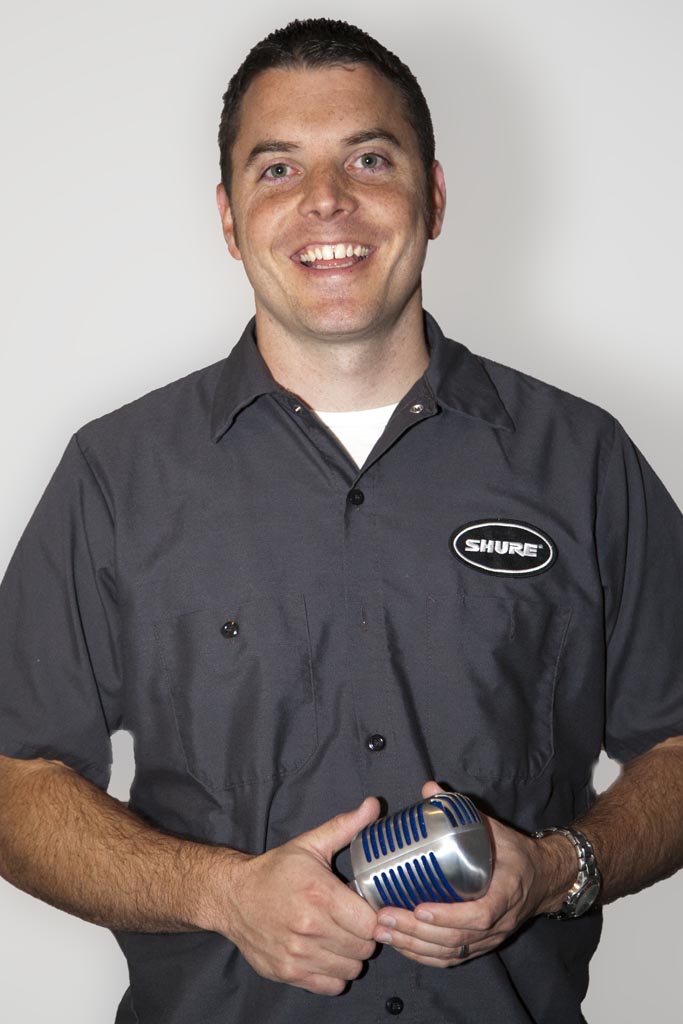
There is a studio, where microphones, instruments and live sound systems can be brought together. Shure conduct blind listening tests of their own product against competitor products. They benchmark each product in the comparison, using good ears sourced from within the company.
Shure have a process to find a critical listener, involving sequencing a track and looped playback. They say that critical listening is an active process, and being Shure they have measured what makes a good listener. “We obtain data from a broad set of listeners,” says John. “But the final decision maker is the product manager,” and that would be John in the case of wired microphones.
Chad Wiggins characterises the job at Shure is – “to produce a design with high levels of reliability. We are a success due to the complexity of our process. And we have to be humble”. Which is as good a credo as we’ve heard anywhere.
Subscribe
Published monthly since 1991, our famous AV industry magazine is free for download or pay for print. Subscribers also receive CX News, our free weekly email with the latest industry news and jobs.