CONTROL
22 Mar 2023
MEYER SOUND’S KATIE MURPHY
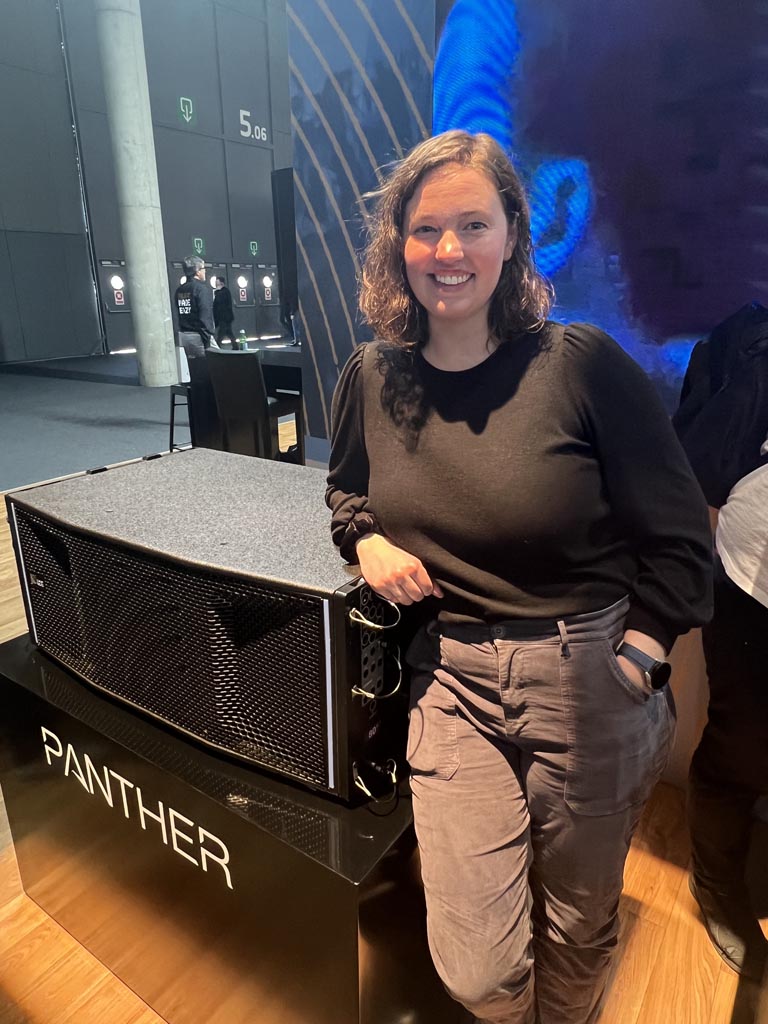
Subscribe to CX E-News
PANTHER, 2100-LFC, and the Future of Loudspeaker Design
Meyer Sound’s Engineering Director – Acoustical and Mechanical Katie Murphy has been with the San Francisco-based manufacturer for just over six years now, and in that time has presided over some major designs and new product releases, including the record-selling PANTHER large-format linear line array loudspeaker.
Proudly flanking their newest release, the 2100-LFC low-frequency control element (which most of us would call a subwoofer and was designed to complement PANTHER and all of Meyer Sound’s line arrays), Katie sat down with me to talk loudspeaker design, advances in technology, and why packing the truck should be the first thing you think about.
So, what career path had led her into the dark art of loudspeaker design? “I was always into my music, and I went to the University of Southern California to study electrical engineering,” explains Katie. “While I was studying, I was working on the side as an audio assistant, then technician, for the school’s performance venues, one of which is Bovard Auditorium, which had recently gotten a new Meyer Sound system. “Along with the electrical engineering major, I got a minor in music recording. I always knew that I wanted to use my engineering degree for something that was going to get me back to music. Then an opportunity came up at Meyer Sound, and here I am!”
As a sane and sensible electrical engineer, does Katie also see loudspeaker design as a realm that is part science and part magic?
“Loudspeaker design can seem like wizardry until you are able to understand some of the ways that sound is unpredictable,” observes Katie. “What I’ve learned is that sometimes sound is unpredictable in a predictable manner. I was lucky to start my career at Meyer Sound in acoustic testing. We were asking ourselves ‘how do we create a blind test that is valid and tests the unit for the performance that matters?’ When you start with that, you gain an understanding that ‘one plus one does not necessarily equal two’ in a product. You have to design the product for the performance you need in the field and work your way back.”
As this magazine goes to print, this author is likely standing in front of 212 elements of Katie’s work in the form of PANTHER as the huge Ed Sheeran “+ – = ÷ x” (“Mathematics”) Tour stops in Melbourne. UK production firm Major Tom adopted PANTHER for the tour, with the PA making its debut in Dublin in April 2022. Both Major Tom and Meyer Sound are serious about reducing their environmental footprint, and this thinking has been crucial to the development of both PANTHER and the 2100-LFC.
“One of the first things we think of when designing a touring product is the truck pack,” outlines Katie. “Andy Davies, our Senior Product Manager, is very good at reminding the team, anytime we start to talk about how to size something, how many can go on a caster, how many caster stacks can go in a truck. This really matters; this is no longer one of the considerations that are lower down the list of priorities. We started designing PANTHER and the 2100-LFC with an exact number that needed to fit on one truck. And we’ve achieved that; the recent Michael Bublé tour had the entire Meyer Sound PA in one truck.”

The environmental and economic imperative of fewer trucks on tours is becoming more important as costs rise and artists and their management become more aware of their carbon footprint. Meyer Sound is meeting these 21st century challenges through design- based solutions. “What we’re trying to do is take the previous generation of products and make them smaller, fit in both European and American trucks, gain more power while being more efficient, and improve sonic performance” states Katie. “There are two ways to achieve this; pick a performance class above and size down, or pick something you already have and make it smaller. For example, when we designed the 2100-LFC, we started by looking at the 1100-LFC. . The 1100-LFC is a powerhouse and helped set the standard for a generation of products. We said, let’s take that as a starting point, make it more compact and lighter, with a new amp and new drivers. Now we have a product that you can use where you could have used an 1100-LFC, works with every Meyer Sound system both existing and future-facing, and is in the same performance class.”
With both PANTHER and the 2100-LFC achieving SPL outputs previously only possible with larger, heavier loudspeakers, where are the weight and power efficiencies coming from? “Some of the biggest advances in technology recently have been in materials,” divulges Katie. “We’re sourcing materials that weigh less but offer the same performance and reliability, which allow us to make things smaller but still get the same, if not more, power. We’re now using aluminium where we once used steel, in both the rigging and internal structure. We have found we can use thinner wood that our structural engineers confirm is just as strong.”
Another weight saver has been the adoption of Milan AVB signal distribution, and the change from analog to digital amplifier technology. “The transformer of a LEO line array element weighs more than the entire amplifier chassis of a PANTHER,” confirms Katie. “We’ve also been able to improve our driver materials. Between the magnets and the different pieces of metal that go into a magnetic structure, if you reduce the weight of every single piece a little by using cutting-edge tech, the whole comes out much lighter.”
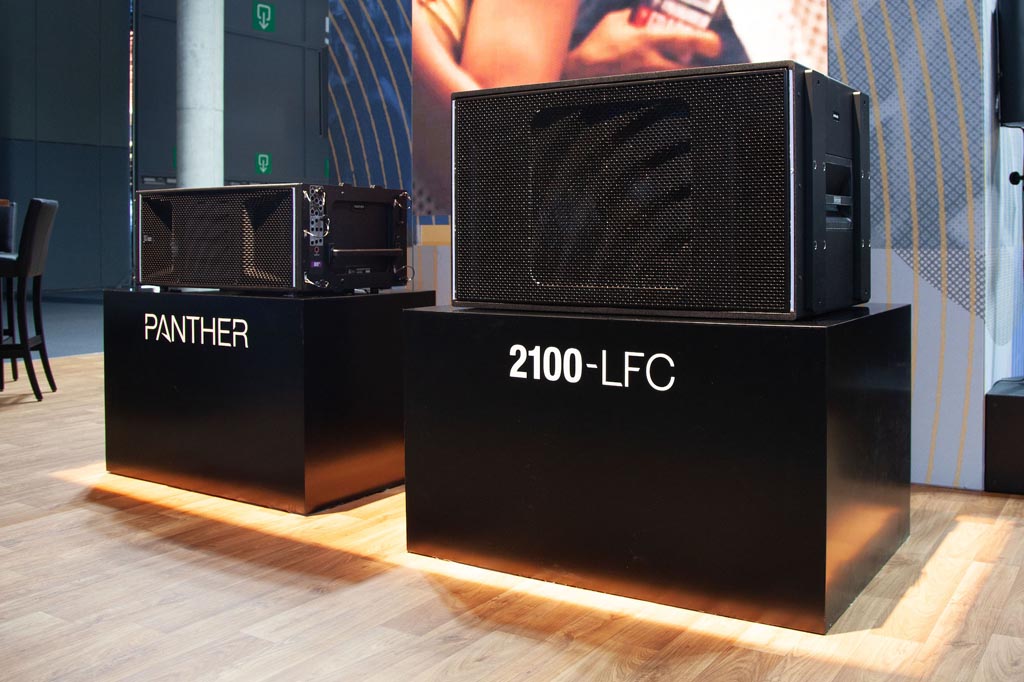
Both PANTHER and the 2100-LFC join the Meyer Sound Milan AVB environment that is connected and monitored via their new software platform, Nebra. “When we’re developing a new product, we’re not just looking at releasing that one product, we’re thinking of what ecosystem is best for it to fit in,” Katie elucidates. “What are our users going to use with it? We want to be future-facing and make sure that all of the standards we set are going to be achievable for the next product.”
Standing in the middle of ISE with 40,000 other AV professionals, the difficulties the industry faced over the last three years feel like they are disappearing into history. “Coming out of the pandemic, the engineering team and Meyer Sound as a whole are working beautifully,” concludes Katie. “We’re all coming together to ensure we’re designing solutions, not just a box. We don’t want to release a box every year just for the heck of it; the industry is now in a place where that no longer makes sense. We’re proud of the fact that we’re introducing a product that the market wants and has been asking for, taking feedback, and then incorporating that into our next product. We feel good about the way we’re doing things.”
Subscribe
Published monthly since 1991, our famous AV industry magazine is free for download or pay for print. Subscribers also receive CX News, our free weekly email with the latest industry news and jobs.